Commercial Real Estate Property
Inspections and Assessments
Serving All Texas Areas
Commercial Property Inspections including but not limited to:
San Antonio, Boerne, San Marcos, Dallas, Fort Worth, New Braunfels, Austin, Georgetown,
Roundrock, Houston, Beaumont, Dilley, Abilene, College Station, Temple, McAllen, Plano,
Texarkana, Padre Island, San Angelo, Tyler, Witchita Falls, Galveston, Midland, Corpus Christi,
El Paso, Waco, Kingsville, Junction, Schertz, Seguin, Kerrville, Crystal City, Nachogdoches,
Fredricksburg, Lubbock, Eagle Pass, Laredo, Brownsville & many more Texas areas.
JWK INSPECTIONS & CONSULTING
210-559-3236 email: joeksatx@gmail.com
Joe Keresztury, JWK Inspections & Consulting
Our Commercial Property Inspection Team shown below:
Brian Schantz Dan Sawatzki Hoyt Pollock
JWK INSPECTIONS & CONSULTING
The San Antonio & South Texas areas # 1 Property Inspector for Many Reasons.
Click above to see our many 5 star Google Reviews
Commercial Real Estate Property & Building Inspections which are also known
as Commercial Property Assessments is important for you the client wanting to know the
condition of the property you are considering or already planning to purchase
or lease. Our commercial inspection standards as outlined below will help you,
the client understand the overall scope based on industry standards of the property inspection
and assessment procedure including detailing of the areas and systems to be inspected.
Once the inspection, the Commercial Property Assessment is completed,
a computer generated Property Condition and Inspection Report with photos will be emailed
to you the client within a time period approved in the agrreement.
The Commercial Property Inspection Report will include items reported as deficiencies,
including items recommended for repairs or suggestions for items in need of
further evaluation by specialists in the field of the noted problem area.
..
..Schedule an Inspection or Request a Qoute - (click)..
.
-
Zip Level, Foundation Level Survey Thermal Imaging / Infrared Camera Drones for Site & Roof Reviews
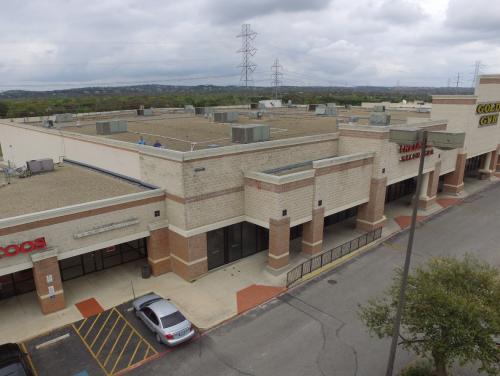
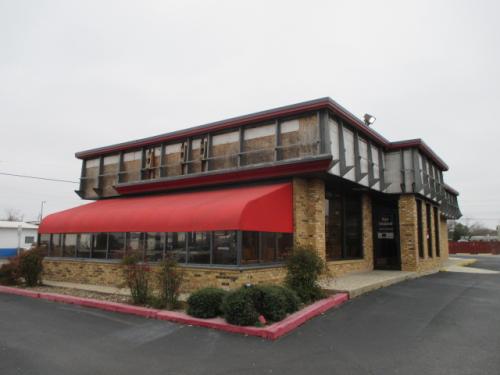
Leon Valley, TX Strip Center Universal City Restauraunt Taft, Texas Apartments
Multi Family Complex- N.C. San Antonio Northwest San Antonio, Office Complex
Three Rivers, Boerne, Leon Valley, Dilley, Universal City, Schertz, Converse and other areas.
Office Building Complex San Antonio NC San Antonio Business Office Center Business Center NE San Antonio
The Drone Photo shows Roof Level readings that were done by the Zip Level System for this
TPO Commercial Property Roof Inspection by JWK Inspections in Downtown San Antonio.
.
Below- 2 Foundation Level Surveys performed by
JWK Inspections
at Commercial Property Strip Centers.
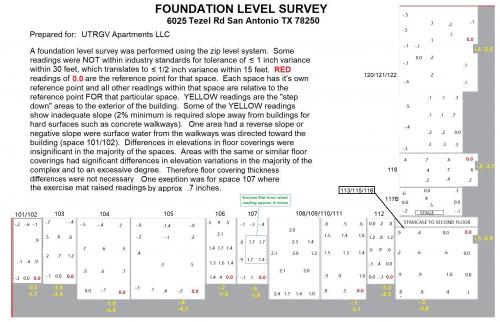
.
.
Your South Central Texas Commercial Property Inspector
Including San Antonio, Austin, San Marcos, Boerne, Houston,
Georgetown, Junction, Corpus Christi, Fredricksburg, Galveston
and all other surrounding areas.
For More Information:
Email:
joeksatx@gmail.com - Call 210.559.3236
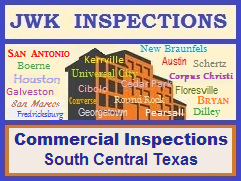
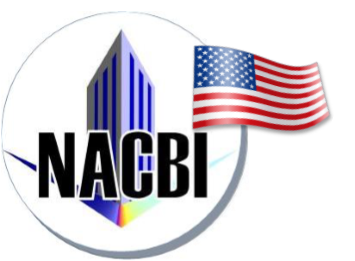
Joe Keresztury is an InterNachi Certified Commercial Property Inspector,
A Network Member of COM INSPECT and
Member of NACBI - The National Association of Commercial Building Inspectors
" I strongly recommend JWK Inspections in San Antonio Texas for all your
home and commercial building inspection needs. Joe is one of the most knowledgeable inspectors
in the state of Texas. Joe's professionalism is reflected in every inspection report he produces
for his clients, call Joe today to schedule an inspection, you will be glad you chose
JWK Inspections for your inspection needs ".
- Dale Duffy
Mr. Duffy is the founder of the:
National Association of Commercial Building Inspectors (NACBI)
Commercial Property Inspection Reviews shown below For JWK Inspections:


For more Reviews see us on Google as
#1 Rated in the San Antonio & South Texas areas. (Click to visit)
Below is our Commercial Property Inspection Standards based on COMINSPECT and InterNACHI
A commercial property is defined as the building structures and improvements located on a parcel of commercial real estate. These may include structures such as buildings with residential units operated for profit, mixed-use buildings, strip malls, motels, factories, storage facilities, restaurants and office buildings.
The inspection is defined as the process of an inspector collecting information through visual observation during a walk-through survey of the subject property, conducting research about the property, and then generating a meaningful report about the condition of the property based on the observations made and research conducted by the inspector. A commercial inspection requires the inspector to make observations, conduct research, and report findings.
Observations are defined as those potential items of interest noted by the inspector during the walk-through survey portion of the inspection.
Research: Research is defined as the process of gathering information through document review and interviews to augment the observations made during the walk-through portion of the inspection. This research may include reviewing readily available documents, such as previous inspection reports, building permits, code violation notices and environmental studies. This research may also include interviews with readily available personnel, such as building managers, tenants and owners.
An inspection report is defined as a written communication describing the issues discovered from observations made and research conducted by the inspector that are, in the inspector's opinion, likely to be of interest to his/her client. A report may contain photographs of observations made during the walk-through survey portion of the inspection and/or copies of documents reviewed during the research portion of the inspection.
The objective of an inspection is to provide written communication describing the issues discovered from observations made and research conducted by the inspector, which, in the inspector's opinion, are likely to be of interest to his/her client, and to enhance the client's information and knowledge about the commercial property to improve decision-making for buying, selling, maintaining or improving the property.
Any portion of the inspection, including the walk-through survey, research and report-generation, may be performed by the inspector, his/her staff, or any consultant hired by the inspector. This Standard recognizes that, for the majority of commercial inspections, the inspector is likely an individual with a general, well-rounded knowledge of commercial properties, and that the inspector or client may want to augment the inspector's skills with specialty consultants who have particular expertise in certain areas. The decision to hire specialty consultants will, of course, rely on budget and time constraints, as well as the risk-tolerance of the client.
This Standard is designed as a baseline from which the inspector and client can develop and agree to a scope of work that may deviate from this Standard, depending on budget, time constraints, purpose of the inspection, age of the subject property, and risk-tolerance of the client. The level of due diligence should be set where the cost, in time and money, of acquiring information about the subject property will not likely exceed the value of that information. Therefore, an inspection performed in accordance with this Standard will not be technically exhaustive.
The client should understand that no inspection report is completely accurate. A report is only the written communication of the observations made and research conducted by the inspector. The report contains those items which, in the inspector's opinion, are likely to be of interest to his/her client.
The client should understand that the inspection report is, to a large degree, the subjective opinions of the inspector based on his/her observations and research within the limits of access, time and budget, and without the aid of special equipment or meters, and without dismantling, probing, testing or troubleshooting, and without detailed knowledge of the commercial property, its components or its systems. The inspection report is not much more than a subjective professional opinion.
An inspector performing a commercial inspection in accordance with this Standard is not practicing architecture or engineering. Not a Warranty, Guarantee or Insurance PolicyThe inspection is not a warranty, and the inspection report is merely the written communication of the inspector's subjective opinion on the condition of the subject property.
The objective of research, including the review of documents and the performing of interviews, is to augment the information obtained during the walk-through survey and to provide supporting documentation to the inspection report.It is the client's responsibility to obtain copies of all documents and provide them for the inspector. These documents are most often obtained from the seller or from local government offices. The inspector is not responsible for gathering or paying for copies of appropriate documents to be reviewed unless these tasks are specifically assigned to the inspector in the Scope of Work Agreement.
The inspector should review all documents provided by the client and owner. The inspector should also make an inquiry and review of any other documents that can be reasonably procured on-site or from the building owner or manager, such as Certificates of Occupancy, building code violation notices, repair invoices, and warranties. The inspector is not required to uncover and review information that is not provided or cannot be reasonably ascertained or acquired on-site. Copies of documents that the inspector believes may be of interest to the client and copies of documents that support the inspector's opinions should be included in the inspection report.
Some of the documents the inspector will review at clients request include:
accessibility surveys, appraisals, building plans, Certificates of Occupancy, citations,
deck age records, plans and construction permits;
deck and balcony maintenance, power-washing, painting, treating, repair and modification history;
emergency evacuation plans; environmental studies; evacuation drill records;
fire-detection test and maintenance records; fire door inspection reports; fire-prevention plans;
fire extinguisher service records; fire records;flame-resistant certificates; flood plain maps/plats;
floor plans; bluerints, engineered designs,
kitchen grease-cleaning records; kitchen post-fire inspections;
maintenance records; manufacturers' installation instructions;
notices; permits; power-washing records; previous inspection reports;
proposals; rent records; repair estimates/invoices; safety inspection records;
seller disclosures; sprinkler head replacement records;
utility bills; and warranties.
The inspector should identify and interview the person(s) with the most knowledge about the condition of the building. Typically, this will be the building owner or manager. Unless otherwise agreed to in the Scope of Work Agreement, it is the responsibility of the client to arrange to have such person(s) on hand for interview by the inspector on the day of the walk-through survey.
The inspector may request that the owner, building manager and/or client fill out pre-inspection questionnaires to gather information. The inspector may rely that these responses are truthful. In cases where parties refuse to fill out questionnaires in writing, the inspector may interview the parties and fill out the questionnaires for them. The inspector should note in the report if s/he filled out the questionnaire based on an interview and whether such interview was performed in person, by telephone, or by email. Copies of all responses to such questionnaires should be included in the inspection report.
The level of accuracy of information varies, depending on its source. The inspector may rely on information obtained to the extent that the information appears to be accurate and complete. This Standard does not require the inspector to independently verify the accuracy of the documents reviewed by the inspector or included in the report, nor the statements made by those interviewed by the inspector.
The inspector is not a fraud investigator, and this Standard does not require the inspector to look for intentionally hidden deficiencies in the subject property. The inspection report is supplementary to the seller's disclosures.
It is the client's responsibility to arrange for the inspector to receive timely access to the subject property for the walk-through survey portion of the inspection, as well as access to all documents and interviewees needed for the research portion of the inspection. This includes access to all documents, information and previously generated reports in the client's possession. The inspector is not responsible for obtaining, reviewing or providing information, should the source withhold, impede or delay access. Anything that hinders the inspector's access should be noted in the report.
The inspector should inspect :
A. the roof covering;
The Inspector should inspect form ground level, eaves
or rooftop (if a roof top door access exists).
The inspector is not required to:
A. walk on any pitched roof surface. B. predict service-life expectancy.
C. inspect underground downspout diverter drainage pipes. D. remove snow, ice, debris or other conditions that prohibit the observation of the roof surfaces.
E. move insulation. F. inspect antennae, lightning arresters, de-icing equipment or similar attachments.
G. walk on any roof areas that appear, in the opinion of the inspector, to be unsafe. H. walk on any roof areas if it might, in the opinion of the inspector, cause damage.
I. perform a water test. J. warrant or certify the roof. K. walk on any roofs that lack rooftop access doors.
Exterior- 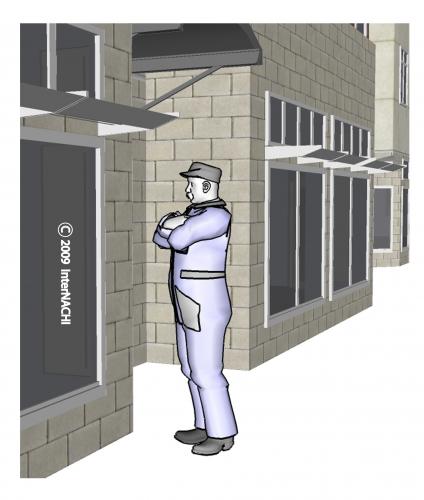
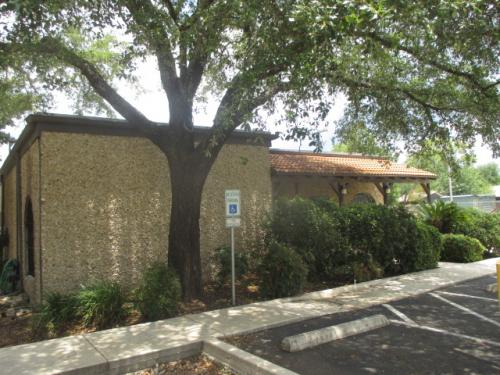
The inspector should inspect:
A. the siding, flashing and trim;
B. all exterior doors, decks, stoops, steps, stairs, porches, railings, eaves, soffits and fasciae;
C. and report as in need of repair any safety issues regarding intermediate balusters, spindles or rails for steps, stairways, balconies and railings;
D. a representative number of windows;
E. the vegetation, surface drainage, and retaining walls when these are likely to adversely affect the structure;
F. the exterior for accessibility barriers;
G. the storm water drainage system;
H. the general topography;
I. the parking areas;
J. the sidewalks;
K. exterior lighting;
L. the landscaping;
M. and determine that a 3-foot clear space exists around the circumference of fire hydrants;
N. and describe the exterior wall covering.
The inspector is not required to:
A. inspect or operate screens, storm windows, shutters, awnings, fences, outbuildings or exterior accent lighting.
B. inspect items, including window and door flashings, that are not visible or readily accessible from the ground.
C. inspect geological, geotechnical, hydrological or soil conditions.
D. inspect recreational facilities.
E. inspect seawalls, breakwalls or docks.
F. inspect erosion-control or earth-stabilization measures.
G. inspect for proof of safety-type glass.
H. determine the integrity of thermal window seals or damaged glass.
I. inspect underground utilities.
J. inspect underground items.
K. inspect wells or springs.
L. inspect solar systems.
M. inspect swimming pools or spas.
N. inspect septic systems or cesspools.
O. inspect playground equipment.
P. inspect sprinkler systems.
Q. inspect drainfields or dry wells.
R. inspect manhole covers.
S. operate or evaluate remote-control devices, or test door or gate operators.
Wood Decks and Balconies- 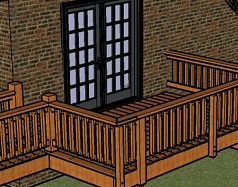
The inspector should inspect
A. with the unaided eye, for deck and balcony members that are noticeably out of level or out of plumb;
B. for visible decay;
C. for paint failure and buckling;
D. for nail pullout (nail pop);
E. for fastener rust, iron stain and corrosion;
F. and verify that flashing was installed on the deck-side of the ledger board;
G. for vertical members (posts) that have exposed end-grains;
H. for obvious trip hazards;
I. for non-graspable handrails;
J.. railings for height less than the 36-inch minimum*;
K. guardrails and infill for openings that exceed the 4-inch maximum*;
L. open-tread stairs for openings that exceed the 4⅜-inch maximum*;
M. the triangular area between guardrails and stairways for openings that exceed the 6-inch maximum*;
N. built-up and multi-ply beam spans for butt joints;
O. for notches in the middle-third of solid-sawn wood spans;
P. for large splits longer than the depths of their solid-sawn wood members;
Q. for building egresses blocked, covered or hindered by deck construction; and
R. for the possibility of wetting from gutters, downspouts or sprinklers.
The inspector is not required to:
A. discover insect infestation or damage.
B. inspect, determine or test the tightness or adequacy of fasteners.
C. determine lumber grade.
D. measure moisture content.
E. inspect for or determine bending strength.
F. inspect for or determine shear stress.
G. determine lag screw or bolt shear values.
H. calculate loads.
I. determine proper spans or inspect for deflections.
J. discover decay hidden by paint.
K. verify that flashing has been coated to prevent corrosion.
L. determine that post-to-footing attachments exist.
M. dig below grade or remove soil around posts.
N. crawl under any deck with less than 3 feet of headroom, or remove deck skirting to acquire access.
O. determine proper footing depth or frostline.
P. verify proper footing size.
Q. perform pick tests.
R. perform or provide any architectural or engineering service.
S. use a level or plumb bob.
T. use a moisture meter.
U. predict service-life expectancy.
V. verify compliance with permits, codes or formal standards.
W. inspect for disabled persons' accessibility barriers.
X. determine if a deck blocks, covers or hinders septic tank or plumbing access.
Y. determine easement-encroachment compliance.
Foundation and Crawlspace- 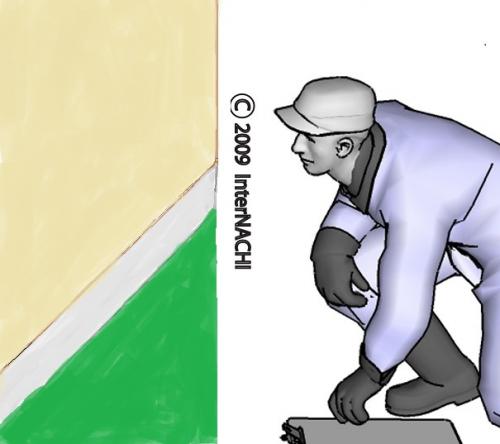
The inspector should inspect:
A. the basement;
B. the foundation;
C. the crawlspace;
D. the visible structural components;
E. and report on the location of under-floor access openings;
F. and report any present conditions or clear indications of active water penetration observed by the inspector;
G. for wood in contact with or near soil;
H. and report any general indications of foundation movement that are observed by the inspector, such as, but not limited to: sheetrock cracks, brick cracks, out-of-square door frames, or floor slopes;
I. and report on any cutting, notching or boring of framing members that may present a structural or safety concern.
The inspector is not required to:
A. enter any crawlspaces that are not readily accessible, or where entry could cause damage or pose a hazard to the inspector.
B. move stored items or debris.
C. operate sump pumps.
D. identify size, spacing, span or location, or determine the adequacy of foundation bolting, bracing, joists, joist spans or support systems.
E. perform or provide any engineering or architectural service.
F. report on the adequacy of any structural system or component.
Heating and Ventilation 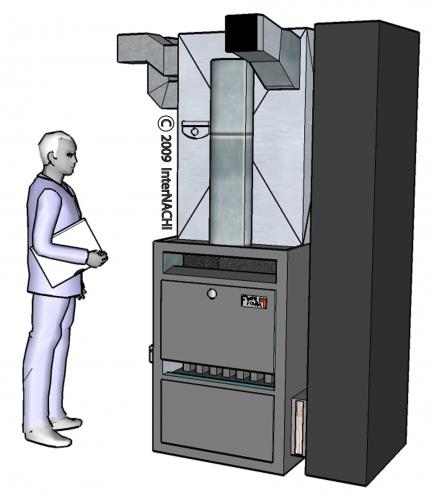
The inspector should inspect:
A. multiple gas meter installations, such as a building with multiple tenant spaces, and verify that each meter is clearly and permanently identified with the respective space supplied;
B. the heating systems using normal operating controls, and describe the energy source and heating method;
C. and report as in need of repair heating systems that do not operate;
D. and report if the heating systems are deemed inaccessible;
E. and verify that a permanent means of access, with permanent ladders and/or catwalks, are present for equipment and appliances on roofs higher than 16 feet;
F. and verify the presence of level service platforms for appliances on roofs with a slope of 25% or greater;
G. and verify that luminaire and receptacle outlets are provided at or near the appliance;
H. and verify that the system piping appears to be sloped to permit the system to be drained;
I. for connectors, tubing and piping that might be installed in a way that exposes them to physical damage;
J. wood framing with cutting, notching or boring that might cause a structural or safety issue;
K. pipe penetrations in concrete and masonry building elements to verify that they are sleeved;
L. exposed gas piping for identification by a yellow label marked "Gas" in black letters occurring at intervals of 5 feet or less;
M. and determine if any appliances or equipment with ignition sources are located in public, private, repair or parking garages or fuel-dispensing facilities;
N. and verify that fuel-fired appliances are not located in or obtain combustion air from sleeping rooms, bathrooms, storage closets or surgical rooms;
O. for the presence of exhaust systems in occupied areas where there is a likelihood of excess heat, odors, fumes, spray, gas, noxious gases or smoke;
P. and verify that outdoor air-intake openings are located at least 10 feet away from any hazardous or noxious contaminant sources, such as vents, chimneys, plumbing vents, streets, alleys, parking lots or loading docks;
Q. outdoor exhaust outlets for the likelihood that they may cause a public nuisance or fire hazard due to smoke, grease, gases, vapors or odors;
R. for the potential of flooding or evidence of past flooding that could cause mold in ductwork or plenums; and
S. condensate drains.
The inspector is not required to:
A. inspect or evaluate interiors of flues or chimneys, fire chambers, heat exchangers, humidifiers, dehumidifiers, electronic air filters, solar heating systems, fuel tanks, safety devices, pressure gauges, or control mechanisms.
B. determine the uniformity, temperature, flow, balance, distribution, size, capacity, BTU, or supply adequacy of the heating system.
C. light or ignite pilot flames.
D. activate heating, heat pump systems, or other heating systems when ambient temperatures or other circumstances are not conducive to safe operation or may damage the equipment.
E. over-ride electronic thermostats.
F. evaluate fuel quality.
G. verify thermostat calibration, heat anticipation or automatic setbacks, timers, programs or clocks.
H. inspect tenant-owned or tenant-maintained heating equipment.
I. determine ventilation rates.
J. perform capture and containment tests.
K. test for mold.
Cooling-
The inspector should inspect:
A. multiple air-conditioning compressor installations, such as a building with multiple tenant spaces, and verify that each compressor is clearly and permanently identified with the respective space supplied;
B. the central cooling equipment using normal operating controls;
C. and verify that luminaire and receptacle outlets are provided at or near the appliance;
D. and verify that a permanent means of access, with permanent ladders and/or catwalks, are present for equipment and appliances on roofs higher than 16 feet;
E. and verify the presence of level service platforms for appliances on roofs with a slope of 25% or greater;
F. wood framing with cutting, notching or boring that might cause a structural or safety issue;
G. pipe penetrations in concrete and masonry building elements to verify that they are sleeved;
H. piping support;
I. for connectors, tubing and piping that might be installed in a way that exposes them to physical damage;
J. for the potential of flooding or evidence of past flooding that could cause mold in ductwork and plenums; and K. condensate drains.
The inspector is not required to:
A. inspect or test compressors, condensers, vessels, evaporators, safety devices, pressure gauges, or control mechanisms.
B. determine the uniformity, temperature, flow, balance, distribution, size, capacity, BTU, or supply adequacy of the cooling system.
C. inspect window units, through-wall units, or electronic air filters.
D. operate equipment or systems if exterior temperature is below 60° Fahrenheit, or when other circumstances are not conducive to safe operation or may damage the equipment.
E. inspect or determine thermostat calibration, cooling anticipation, or automatic setbacks or clocks.
F. examine electrical current, coolant fluids or gases, or coolant leakage.
G. inspect tenant-owned or tenant-maintained cooling equipment.
H. test for mold.
Plumbing- 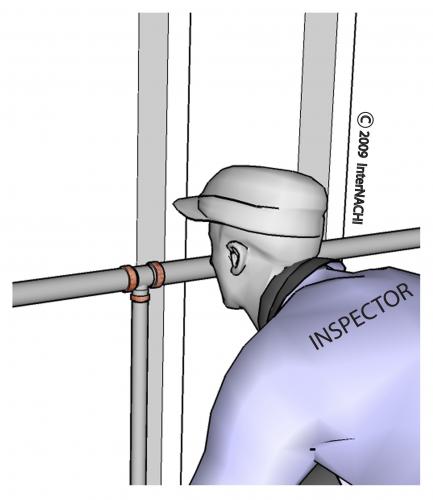
The inspector should inspect:
A. and verify the presence of and identify the location of the main water shut-off valve to each building;
B. and verify the presence of a back-flow prevention device if, in the inspector's opinion, a cross-connection could occur between the water-distribution system and non-potable water or private source;
C. the water-heating equipment, including combustion air, venting, connections, energy-source supply systems, and seismic bracing, and verify the presence or absence of temperature-/pressure-relief valves and/or Watts 210 valves;
D. and flush a representative number of toilets;
E. and water-test a representative number of sinks, tubs and showers for functional drainage;
F. and verify that hinged shower doors open outward from the shower, and have safety glass-conformance stickers or indicators;
G. the interior water supply, including a representative number of fixtures and faucets;
H. the drain, waste and vent systems, including a representative number of fixtures;
I. and describe any visible fuel-storage systems;
J. and test sump pumps with accessible floats;
K. and describe the water supply, drain, waste and main fuel shut-off valves, as well as the location of the water main and main fuel shut-off valves;
L. and determine whether the water supply is public or private;
M. the water supply by viewing the functional flow in several fixtures operated simultaneously, and report any deficiencies as in need of repair;
N. and report as in need of repair deficiencies in installation and identification of hot and cold faucets;
O. and report as in need of repair mechanical drain stops that are missing or do not operate if installed in sinks, lavatories and tubs;
P. and report as in need of repair commodes that have cracks in the ceramic material, are improperly mounted on the floor, leak, or have tank components that do not operate; and
Q. piping support.
The inspector is not required to:
A. determine the adequacy of the size of pipes, supplies, vents, traps or stacks.
B. ignite pilot flames.
C. determine the size, temperature, age, life expectancy or adequacy of the water heater.
D. inspect interiors of flues or chimneys, cleanouts, water-softening or filtering systems, dishwashers, interceptors, separators, sump pumps, well pumps or tanks, safety or shut-off valves, whirlpools, swimming pools, floor drains, lawn sprinkler systems or fire sprinkler systems.
E. determine the exact flow rate, volume, pressure, temperature or adequacy of the water supply.
F. verify or test anti-scald devices.
G. determine the water quality, potability or reliability of the water supply or source.
H. open sealed plumbing access panels.
I. inspect clothes washing machines or their connections.
J. operate any main, branch or fixture valve.
K. test shower pans, tub and shower surrounds, or enclosures for leakage.
L. evaluate compliance with local or state conservation or energy standards, or the proper design or sizing of any water, waste or venting components, fixtures or piping.
M. determine the effectiveness of anti-siphon, back-flow prevention or drain-stop devices.
N. determine whether there are sufficient cleanouts for effective cleaning of drains.
O. evaluate gas, liquid propane or oil-storage tanks.
P. inspect any private sewage waste-disposal system or component within such a system.
Q. inspect water-treatment systems or water filters.
R. inspect water-storage tanks, pressure pumps, ejector pumps, or bladder tanks.
S. evaluate wait time for hot water at fixtures, or perform testing of any kind on water-heater elements.
T. evaluate or determine the adequacy of combustion air.
U. test, operate, open or close safety controls, manual stop valves, or temperature- or pressure-relief valves.
V. examine ancillary systems or components, such as, but not limited to, those relating to solar water heating or hot-water circulation.
W. determine the presence or condition of polybutylene plumbing.
Electrical 
The inspector should inspect:
A. the service drop/lateral;
B. the meter socket enclosures;
C. the service-entrance conductors, and report on any noted deterioration of the conductor insulation or cable sheath;
D. the means for disconnecting the service main;
E. the service-entrance equipment, and report on any noted physical damage, overheating or corrosion;
F. and determine the rating of the service disconnect amperage, if labeled;
G. panelboards and over-current devices, and report on any noted physical damage, overheating, corrosion, or lack of accessibility or working space (minimum 30 inches wide, 36 inches deep, and 78 inches high in front of panel) that would hamper safe operation, maintenance or inspection;
H. and report on any unused circuit-breaker panel openings that are not filled;
I. and report on absent or poor labeling;
J. the service grounding and bonding;
K. a representative number of switches, lighting fixtures and receptacles, including receptacles observed and deemed to be AFCI-protected using the AFCI test button, where possible. Although a visual inspection, the removal of faceplates or other covers or luminaires (fixtures) to identify suspected hazards is permitted;
L. and report on any noted missing or damaged faceplates or box covers;
M. and report on any noted open junction boxes or open wiring splices;
N. and report on any noted switches and receptacles that are painted;
O. and test all ground-fault circuit interrupter (GFCI) receptacles and GFCI circuit breakers observed and deemed to be GFCIs using a GFCI tester, where possible;
P. and report the presence of solid-conductor aluminum branch-circuit wiring, if readily visible;Q. and report on any tested GFCI receptacles in which power was not present, polarity was incorrect, the cover was not in place, the GFCI devices were not installed properly or did not operate properly, any evidence of arcing or excessive heat, or where the receptacle was not grounded or was not secured to the wall;
R. and report the absence of smoke detectors;
S. and report on the presence of flexible cords being improperly used as substitutes for the fixed wiring of a structure or running through walls, ceilings, floors, doorways, windows, or under carpets.
The inspector is not required to:
A. insert any tool, probe or device into the main panelboard, sub-panels, distribution panelboards, or electrical fixtures.
B. operate electrical systems that are shut down.
C. remove panelboard cabinet covers or dead fronts if they are not readily accessible.
D. operate over-current protection devices.
E. operate non-accessible smoke detectors.
F. measure or determine the amperage or voltage of the main service equipment, if not visibly labeled.
G. inspect the fire or alarm system and components.
H. inspect the ancillary wiring or remote-control devices.
I. activate any electrical systems or branch circuits that are not energized.
J. operate or reset overload devices.
K. inspect low-voltage systems, electrical de-icing tapes, swimming pool wiring, or any time-controlled devices.
L. verify the service ground.
M. inspect private or emergency electrical supply sources, including, but not limited to: generators, windmills, photovoltaic solar collectors, or the battery- or electrical-storage facility.
N. inspect spark or lightning arrestors.
O. inspect or test de-icing equipment.
P. conduct voltage-drop calculations.
Q. determine the accuracy of labeling.
R. inspect tenant-owned equipment.
S. inspect the condition of or determine the ampacity of extension cords.
Fireplaces- 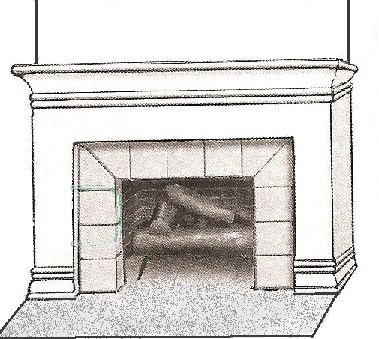
The inspector should inspect:
A. fireplaces, and open and close the damper doors, if readily accessible and operable;
B. hearth extensions and other permanently installed components;
C. and report as in need of repair deficiencies in the lintel, hearth or material surrounding the fireplace, including clearance from combustible materials.
The inspector is not required to:
A. inspect the flue or vent system.
B. inspect the interior of chimneys or flues, fire doors or screens, seals or gaskets, or mantels.
C. determine the need for a chimney sweep.D. operate gas fireplace inserts. E. light pilot flames. F. inspect automatic fuel-feed devices.
G. inspect combustion and/or make-up air devices. H. inspect heat-distribution assists, whether gravity-controlled or fan-assisted.
I. ignite or extinguish fires. J. determine draft characteristics. K. move fireplace inserts, stoves or firebox contents.
L. determine the adequacy of drafts, perform a smoke test, or dismantle or remove any fireplace component.
M. perform an NFPA inspection. N. perform a Phase I fireplace and chimney inspection. O. determine the appropriateness of any installation.
Attic Ventilation and Insulation- 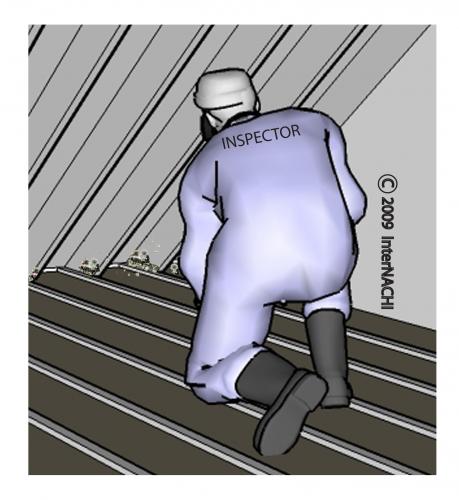
The inspector should inspect:
A. the insulation in unfinished spaces;
B. the ventilation of attic spaces;
C. mechanical ventilation systems;
D. and report on the general absence or lack of insulation.
The inspector is not required to:
A. enter the attic or any unfinished spaces that are not readily accessible, or where entry could cause damage or pose a safety hazard to the inspector, in his or her opinion.
B. move, touch or disturb insulation.C. move, touch or disturb vapor retarders.
D. break or otherwise damage the surface finish or weather seal on or around access panels or covers.
E. identify the composition or exact R-value of insulation material.
F. activate thermostatically operated fans.
G. determine the types of materials used in insulation or wrapping of pipes, ducts, jackets, boilers or wiring.H. determine the adequacy of ventilation.
Doors, Windows and Interior-
The inspector should:
A. open and close a representative number of doors and windows;
B. inspect the walls, ceilings, steps, stairways and railings;
C. inspect garage doors and garage door-openers;D. inspect interior steps, stairs and railings;
E. inspect all loading docks;
F. ride all elevators and escalators;
G. and report as in need of repair any windows that are obviously fogged or display other evidence of broken seals.
The inspector is not required to:
A. inspect paint, wallpaper, window treatments or finish treatments.
B. inspect central-vacuum systems. C. inspect safety glazing.
D. inspect security systems or components.
E. evaluate the fastening of countertops, cabinets, sink tops or fixtures, or firewall compromises.
F. move furniture, stored items, or any coverings, such as carpets or rugs, in order to inspect the concealed floor structure.
G. move drop-ceiling tiles.H. inspect or move any appliances.
I. inspect or operate equipment housed in the garage, except as otherwise noted.
J. verify or certify safe operation of any auto-reverse or related safety function of a garage door.
K. operate or evaluate any security bar-release and opening mechanisms, whether interior or exterior, including their compliance with local, state or federal standards.
L. operate any system, appliance or component that requires the use of special keys, codes, combinations or devices.
M. operate or evaluate self-cleaning oven cycles, tilt guards/latches, gauges or signal lights.
N. inspect microwave ovens, or test leakage from microwave ovens.
O. operate or examine any sauna, steam-jenny, kiln, toaster, ice maker, coffee maker, can opener, bread warmer, blender, instant hot-water dispenser, or other ancillary devices.
P. inspect elevators. Q. inspect remote controls. R. inspect appliances. S. inspect items not permanently installed.
T. examine or operate any above-ground, movable, freestanding, or otherwise non-permanently installed pool/spa, recreational equipment, or self-contained equipment.
U. come into contact with any pool or spa water in order to determine the system's structure or components.
V. determine the adequacy of a spa's jet water force or bubble effect.
W. determine the structural integrity or leakage of a pool or spa.
X. determine combustibility or flammability. Y. inspect tenant-owned equipment or personal property.
Life Safety-
The inspector should :
A. inspect fire access roads and report on any obstructions or overhead wires lower than 13 feet and 6 inches;
B. inspect the address or street number to determine whether it is visible from the street, with numbers in contrast to their background; C. inspect to determine whether a 3-foot clear space exists around the circumference of fire hydrants; D. verify that hinged shower doors open outward from the shower and have safety glass-conformance stickers or indicators; E. inspect to determine whether the storage of flammable and combustible materials is orderly, separated from heaters by distance or shielding so that ignition cannot occur, and not stored in exits, boiler rooms, mechanical rooms or electrical equipment rooms; F. inspect to determine whether a "No Smoking" sign is posted in areas where flammable or combustible material is stored, dispensed or used; G. inspect for the presence of fire alarm systems; H. inspect for alarm panel accessibility; I. inspect for the presence of portable extinguishers, and determine whether they are located in conspicuous and readily available locations immediately available for use, and not obstructed or obscured from view; J. inspect to determine whether a portable fire extinguisher is stored within a 30-foot travel distance of commercial-type cooking equipment that uses cooking oil or animal fat; K. inspect to determine whether manual-actuation devices for commercial cooking appliances exist near the means of egress from the cooking area, 42 to 48 inches above the floor and 10 and 20 feet away, and clearly identifying the hazards protected; L. inspect to determine whether the maximum travel distance to a fire extinguisher is 75 feet; M. inspect for the presence of sprinkler systems, and determine if they were ever painted other than at the factory; N. inspect for the presence of emergency lighting systems; O. inspect for exit signs at all exits, and inspect for independent power sources, such as batteries; P. inspect for the presence of directional signs where an exit location is not obvious; Q. inspect for the presence of signs over lockable exit doors stating: "This Door Must Remain Unlocked During Business Hours"; R. inspect for penetrations in any walls or ceilings that separate the exit corridors or stairwells from the rest of the building; S. inspect for fire-separation doors that appear to have been blocked or wedged open, or that do not automatically close and latch; T. inspect exit stairwell handrails; U. inspect for exit trip hazards; V. inspect for the presence of at least two exits to the outside, or one exit that has a maximum travel distance of 75 feet; W. inspect exit doorways to determine that they are less than 32 inches in clear width; X. inspect to determine whether the exit doors were locked from the inside, chained, bolted, barred, latched or otherwise rendered unusable at the time of the inspection; Y. inspect to determine whether the exit doors swing open in the direction of egress travel; and Z. inspect the storage to determine if it is potentially obstructing access to fire hydrants, fire extinguishers, alarm panels or electric panelboards, or if it is obstructing aisles, corridors, stairways or exit doors, or if it is within 18 inches of sprinkler heads, or if it is within 3 feet of heat-generating appliances or electrical panelboards.
The inspector is not required to:
A. test alarm systems, or determine if alarms systems have been tested.
B. inspect or test heat detectors, fire-suppression systems, or sprinkler systems.
C. determine the combustibility or flammability of materials in storage.
D. determine the adequate number of fire extinguishers needed, or their ratings.
E. test or inspect fire extinguishers, their pressure, or for the presence of extinguisher inspection tags or tamper seals.
F. inspect or test fire pumps or fire department connections.
G. inspect or test cooking equipment suppression systems.H. determine the operational time of emergency lighting or exit signs.
I. inspect for proper occupant load signs. J. determine fire ratings of walls, ceilings, doors, etc.
K. inspect, test or determine the adequacy of fire escapes or ladders.
L. inspect fire department lock boxes or keys. M. determine the flame resistance of curtains or draperies.
N. inspect parking or outdoor lighting.
O. inspect for unauthorized entry or crime issues. P. inspect or test security systems.
Q. inspect for pet or livestock safety issues.
R. inspect for unsafe candle use or decoration hazards.
S. inspect or test emergency generators.
T. test kitchen equipment, appliances or hoods.
U. verfiy that elevator keys exist, or that they work properly.
Cooking Area-
The inspector should i:
A. verify that all smoke- or grease-laden, vapor-producing cooking equipment, such as deep-fat fryers, ranges, griddles, broilers and woks, is equipped with an exhaust system;B. inspect for the accessibility for cleaning and inspection of the exhaust system's interior surface; C. inspect for grease buildup; D. verify that hoods are made of steel or stainless steel;
E. verify that visible grease filters are arranged so that all exhaust air passes through them; F. verify that visible sections of exhaust ducts are not interconnected with any other ventilation system; G. verify that visual sections of exhaust ducts are installed without dips or traps that might collect residue;
H. verify that exhaust ducts do not appear to pass through firewalls; I. try to verify that exhaust ducts lead directly to the exterior of the building;
J. try to verify that exterior exhaust outlets do not discharge into walkways, or create a nuisance, in the opinion of the inspector; K. inspect to determine that a portable fire extinguisher is stored within a 30-foot travel distance of commercial-type cooking equipment that uses cooking oil or animal fat; and L. inspect to determine that manual-actuation devices for commercial cooking appliances exist near the means of egress from the cooking area, 42 and 48 inches above the floor and 10 to 20 feet away, and clearly identifying the hazards protected.
The inspector is not required to:
A. determine proper clearances.
B. determine proper hood size or position. C. test hoods. D. test exhaust fans or dampers, or measure air flow.
E. test fire extinguishers, fire-extinguishing equipment, or fusible links.
F. test kitchen equipment, appliances, hoods or their gauges. G. inspect or test grease-removal devices, drip trays or grease filters.
H. inspect or test air pollution-control devices or fume incinerators. I. inspect or test kitchen refrigeration.
J. inspect for fuel-storage issues. K. inspect, test or determine anything regarding food safety.
L. issue an opinion regarding cooking operating procedures.
7. Report
7.1 Format
The report must be in writing. This Standard does not require any one particular format. It is InterNACHI's opinion that the commercial inspection industry and consumer clients are best served when inspectors are free to compete through report-generation innovation.
7.2 Date
The report should be dated on the first page.
7.3 Inspection Firm Information
The report should include the name and contact information of the inspection firm on the first or second page.
7.4 Property Address
The report should include the address of the property inspected, or a description of the real estate sufficient for identification, on the first or second page.
7.5 Total Number of Pages
The report should indicate the total number of pages and attachments on the first page.
7.6 Brevity
Reports should be concise, to-the-point, and avoid the inclusion of large amounts of pre-printed material.
7.7 Legibility
Reports should be typed or handwritten clearly.
7.8 Opinions of Shut-Down Systems
The inspector should still try to render an opinion of the condition of systems even if they were shut down or were not operational at the time of the walk-through survey.
7.9 Obsolescence
The client should only rely on the inspection report at the point in time that the inspector's observations were being made and research was being conducted. The client should deem the report as obsolete to some extent, even while it is being prepared.
7.10 Site-Specific
The client should understand that an inspection performed in accordance with this Standard only relates to the observations made and research conducted. Consequently, this Standard does not address issues such as business operations at the subject property, deed encumbrances, neighborhood conditions, etc.
7.11 Multiple Buildings
An inspection report produced in accordance with this Standard may encompass more than one building within a single report.
7.12 Cost to Remedy
The inspector is not required to provide repair estimates or opinions of costs to remedy. The inspector may offer opinions about such costs as a courtesy, but the offering of these opinions is outside the scope of a commercial inspection.
8. Limitations, Exceptions and Exclusions
8.1. Limitations:
I. An inspection is not technically exhaustive.
II. An inspection will not identify concealed or latent defects.
III. An inspection will not deal with aesthetic concerns or what could be deemed matters of taste, cosmetic defects, etc.
IV. An inspection will not determine the suitability of the property for any use.
V. An inspection does not determine the market value of the property, or its marketability.
VI. An inspection does not determine the insurability of the property.
VII. An inspection does not determine the advisability or inadvisability of the purchase of the inspected property.
VIII. An inspection does not determine the life expectancy of the property, or any components or systems therein.
IX. An inspection does not include items not permanently installed.
X. These Standards of Practice apply only to commercial properties.
8.2. Exclusions:
I. The inspector is not required to determine:
A. property boundary lines or encroachments.
B. the condition of any component or system that is not readily accessible.
C. the service-life expectancy of any component or system.
D. the size, capacity, BTU, performance or efficiency of any component or system.
E. the cause or reason of any condition.
F. the cause of the need for repair or replacement of any system or component.
G. future conditions.
H. the compliance with codes or regulations.
I. the presence of evidence of rodents, animals or insects.
J. the presence of mold, mildew, fungus or toxic drywall.
K. the presence of airborne hazards.
L. the presence of birds.
M. the presence of other flora or fauna.
N. the air quality.
O. the presence of asbestos.
P. the presence of environmental hazards.
Q. the presence of electromagnetic fields.
R. the presence of hazardous materials including, but not limited to, the presence of lead in paint.
S. any hazardous-waste conditions.
T. any manufacturers' recalls, or conformance with manufacturers' installations, or any information included for consumer-protection purposes.
U. operating costs of systems. V. replacement or repair cost estimates.
W. the acoustical properties of any systems. X. estimates of the cost of operating any given system.
Y. resistance to wind, hurricanes, tornadoes, earthquakes or seismic activities.
Z. geological conditions or soil stability.
II. The inspector is not required to operate:
A. any system that is shut down.
B. any system that does not function properly.
C. or evaluate low-voltage electrical systems, such as, but not limited to:
phone lines;
cable lines;
antennae;
lights; or
remote controls.
D. any system that does not turn on with the use of normal operating controls.
E. any shut off-valves or manual stop valves.
F. any electrical disconnect or over-current protection devices.
G. any alarm systems.
H. moisture meters, gas detectors or similar equipment.
I. sprinkler or fire-suppression systems.
III. The inspector is not required to:
A. move any personal items or other obstructions, such as, but not limited to:
1. throw rugs; 2. furniture; 3. floor or wall coverings;
4. ceiling tiles; 5. window coverings; 6. equipment;
7. plants; 8. ice; 9. debris; 10. snow; 11. water;
12. dirt; 13. foliage; or 14. pets.
B. dismantle, open or uncover any system or component.
C. enter or access any area that may, in the opinion of the inspector, be unsafe.
D. enter crawlspaces or other areas that are unsafe or not readily accessible.
E. inspect or determine the presence of underground items, such as, but not limited to, underground storage tanks, whether abandoned or actively used.
F. do anything which, in the inspector's opinion, is likely to be unsafe or dangerous to the inspector or others, or may damage property, such as, but not limited to, walking on roof surfaces, climbing ladders, entering attic spaces, or interacting with pets or livestock.
G. inspect decorative items.
H. inspect common elements or areas in multi-unit housing.
I. inspect intercoms, speaker systems, radio-controlled, security devices, or lawn-irrigation systems.
J. offer guarantees or warranties. K. offer or perform any engineering services.
L. offer or perform any trade or professional service other than commercial property inspection.
M. research the history of the property, or report on its potential for alteration, modification, extendibility or suitability for a specific or proposed use for occupancy.
N. determine the age of construction or installation of any system, structure or component of a building, or differentiate between original construction and subsequent additions, improvements, renovations or replacements thereto. O. determine the insurability of a property.
P. perform or offer Phase 1 environmental audits.
Q. inspect or report on any system or component that is not included in these Standards.
9. Ethics
Inspectors performing inspections in accordance with this Standard must maintain a high level of business ethics.
9.1 Duty to Client
9.1.1 The inspector shall substantially follow this Standard unless the Scope of Work indicates otherwise.
9.1.2 The inspector shall not engage in any practices that could be damaging to the client or bring discredit to the inspection industry.
9.1.3 The inspector shall be fair, honest, impartial, and act in good faith in dealing with the client.
9.1.4 The inspector shall not discriminate on the basis of race, color, religion, sex, national origin, familial status or handicap, and shall comply with all applicable federal, state and local laws concerning discrimination.
9.1.5 The inspector-member shall be truthful regarding his/her services and qualifications.
9.1.6 The inspector shall have no undisclosed conflict of interest with the client, nor shall the inspector accept or offer any undisclosed commissions, rebates, profits or other benefit, nor shall the inspector accept or offer any disclosed or undisclosed commissions, rebates, profits or other benefit from real estate agents, brokers or any third parties having financial interest in the sale of the property, nor shall the inspector offer or provide any disclosed or undisclosed financial compensation directly or indirectly to any real estate agent, real estate broker or real estate company for referrals or for inclusion on lists of preferred and/or affiliated inspectors or inspection companies.
9.1.7 The inspector shall not communicate any information about an inspection to anyone except the client without the prior written consent of the client, except in cases when the information may affect the safety of others, or violates a law or statute.
9.1.8 The inspector shall always act in the interests of the client, unless doing so violates a law or statute.
9.1.9 The inspector shall use a written Scope of Work Agreement that specifies the services to be performed, the limitations of services, and fees.
9.1.10 The inspector shall comply with all government rules and licensing requirements in the jurisdiction where s/he conducts business.
9.1.11 The inspector shall not perform or offer to perform, for an additional fee, any repairs or repair-associated services to the structure for which the inspector or inspector's company has prepared a commercial inspection report for a period of 12 months. This provision shall not include services to components and/or systems that are not included in this Standard.
END of Standards of Practice
Request for Documents and Person(s) with Knowledge
Dear CLIENT,
Thank you for having JWK Inspections inspect the property at (COMMERCIAL PROPERTY ADDRESS).
On the day of the walk-through survey scheduled for DATE OF WALK-THROUGH SURVEY, I will be doing some research, including the review of documents and the performing of interviews, to augment the information obtained during the walk-through survey, and to provide supporting documentation to the inspection report.
In preparation of the walk-through survey portion of the inspection, please have the seller provide me copies of as many of the following documents as can be reasonably procured:
accessibility surveys;
appraisals;
building plans;
Certificates of Occupancy;
citations;
deck age records, plans and construction permits;
deck and balcony maintenance, power-washing, painting, treating, repair and modification history;
emergency evacuation plans;
environmental studies;
evacuation drill records;
fire-detection test and maintenance records;
fire-door inspection reports;
fire-prevention plans;
fire-extinguisher service records;
fire records;
flame-resistant certificates;
floodplain maps;
floor plans;
kitchen grease-cleaning records;
kitchen post-fire inspections;
maintenance records;
manufacturers' installation instructions;
notices;
permits;
power-washing records;
previous inspection reports;
proposals;
rent records;
repair estimates and/or invoices;
safety inspection records;
seller disclosures;
sprinkler-head replacement records;
utility bills; and
warranties.
I would also like to interview the person(s) with the most knowledge about the condition of the building. Please arrange to have such person(s) on hand on the day of the walk-through survey.
Thank you,
Joseph W. Keresztury
JWK Inspections
CLIENT (Date)
Standard Accessibility Inspection Report
for Existing Commercial Buildings
- About This Accessibility Inspection Report
Various laws around the world require public accommodations to provide goods and services to people with disabilities on an equal basis with the rest of the general public. Businesses benefit from the patronage of all people. Those who own, lease, lease out, or operate places of public accommodation should have as a goal the identification and reduction of physical barriers to this patronage. This inspection report will help identify possible accessibility deficiencies in existing facilities.
Who Must Comply
Most laws regarding accessibility regulate only new construction and remodeling, and do not oblige existing building owners to reduce barriers if such reduction is not readily achievable. This report does not cover all of the possible local, state, provincial or federal requirements regarding accessibility or barrier reduction. The information presented within this report was derived from a visual-only inspection of the property, and is intended solely as informal guidance, and is not a determination of legal rights or responsibilities.
Stand-Alone Inspection Service Option
This report may be offered in conjunction with a complete commercial property inspection, or offered as a separate, stand-alone inspection service.
The Accessibility Inspection Report
Accessibility Inspection Report
Key:
Y = Yes. The statement is true and accessibility appears to be adequate.
N = No. The statement is false and accessibility appears to be deficient.
U = Unknown. Inspector did not determine accessibility.
N/A = Not applicable.
1. Parking
1.1___There are enough accessible parking spaces (8 feet wide plus 5-foot access aisle).
Total number of parking spaces
|
Required number of accessible parking spaces
|
1 to 25
|
1
|
26 to 50
|
2
|
51 to 75
|
3
|
76 to 100
|
4
|
101 to 150
|
5
|
151 to 200
|
6
|
201 to 300
|
7
|
301 to 400
|
8
|
401 to 500
|
9
|
501 to 1,000
|
2% of the total number of parking spaces
|
over 1,000
|
20, plus 1 for each 100 over 1,000
|
1.2___The accessible parking spaces are marked with the International Symbol of Accessibility.
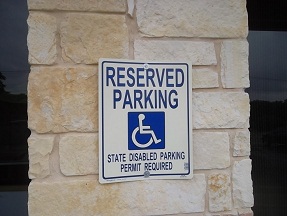
1.3___The accessible parking spaces are the closest spaces to the accessible entrance of the building.
1.4___The accessible parking spaces have access aisles that are part of the accessible route to the accessible entrance of the building.
2. Route of Travel
2.1___There is a route of travel from the accessible parking spaces to the accessible entrance that does not require the use of stairs.
2.2___The route of travel is at least 36 inches wide.
2.3___The slopes on the route of travel are not greater than 5% (1-inch rise/20-inch run).
2.4___The route of travel is stable, firm and slip-resistant.
2.5___The curbs on the route of travel include ramped curb-cuts with a width of at least 36 inches.
3. Ramps
3.1___Ramps longer than 6 feet have railings on both sides.
3.2___Railings are sturdy and between 34 and 38 inches high.
3.3___Ramps are stable, firm and slip-resistant.
3.4___There is a 5-foot-long level landing at the top and bottom of every 30-foot horizontal length of ramp and at every ramp switchback.
4. Entrance
4.1___The main entrance is accessible, or there is a ramp, lift or alternative accessible entrance.
4.2___All inaccessible entrances have signs giving directions to the nearest accessible entrance.
4.3___The accessible entrance door has at least 32 inches of clear opening.
4.4___The accessible entrance door has at least 24 inches of clear wall space on the pull-side of the door next to the handle.
4.5___The accessible entrance door handle is no higher than 48 inches.
4.6___The accessible entrance door handle is operable with a closed fist (accessible to a person with limited use of his/her hands).
4.7___The accessible entrance door can be opened without too much force (less than 8½ pounds of force).
4.8___The accessible entrance threshold is not a trip hazard or wheelchair barrier (less than a ¼-inch high, or less than ¾-inches high with bevels on both sides).
4.9___The automatic door closer (if one exists) on the accessible entrance takes at least three seconds to close the door.
5. Interior
5.1___The interior carpeting is low-pile and tightly woven.
5.2___There are no noted hindrances to a person who uses a cane.
5.3___The corridors are at least 36 inches wide.
5.4___The corridors have wheelchair-passing spaces at reasonable intervals (less than 200 feet), or intersecting corridors that can be used as passing spaces.
6. Restrooms
6.1___Public restrooms include at least one fully accessible restroom on an accessible route of travel.
6.2___The inaccessible restrooms have signs that give directions to accessible ones.
6.3___Pictograms or symbols are used to identify restrooms.
6.4___Accessible restroom door handles are no higher than 48 inches.
6.5___Accessible restroom door handles are operable with a closed fist (accessible to a person with limited use of his/her hands).
6.6___Accessible restroom doors can be opened without too much force (less than 5 pounds of force).
6.7___The accessible restroom entry configuration provides adequate maneuvering and turnaround space (60 inches in diameter) for wheelchairs.
6.8___The path to all fixtures in the accessible restroom is at least 36 inches wide.
6.9___The accessible restroom stall door is operable with a closed fist (accessible to a person with limited use of his/her hands) inside and out.
6.10___The accessible restroom has at least one wheelchair-accessible stall that provides adequate maneuvering space for a wheelchair.
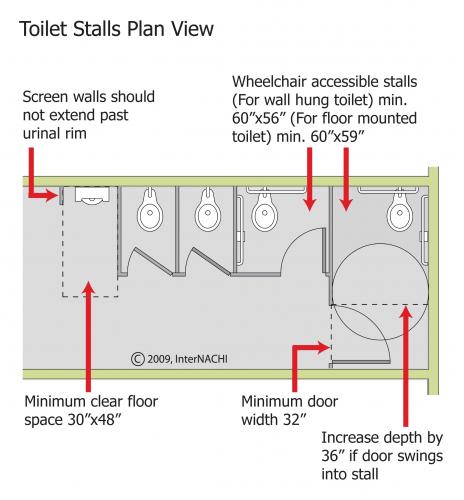
6.11___The wheelchair-accessible stall has grab bars behind and on the side wall nearest the toilet.
6.12___The wheelchair-accessible stall has a toilet seat that is 17 to 19 inches high.
6.13___The wheelchair-accessible stall has a toilet seat that does not spring back to a lifted position.
6.14___The accessible restroom has at least one urinal with a rim no higher than 17 inches above the floor.
6.15___The accessible restroom has at least one lavatory with a 30-inch wide by 48-inch deep clear space in front of it.
6.16___The accessible restroom lavatory has a rim no higher than 34 inches.
6.17___The accessible restroom lavatory has at least 29 inches of knee space between the floor and the bottom of the lavatory apron.
6.18___The accessible restroom lavatory has no hot pipes or sharp surfaces underneath that could harm a person in a wheelchair.
6.19___The accessible restroom lavatory faucet can be operated with one closed fist (accessible to a person with limited use of his/her hands).
6.20___The accessible restroom lavatory faucet (if self-closing) permits the water to flow for at least 10 seconds.
6.21___The accessible restroom soap dispensers and hand dryers are within reach of a person in a wheelchair, and are operable with one closed fist.
6.22___The accessible restroom mirror (if provided) is mounted with the bottom edge of the reflecting surface no higher than 40 inches.
7. Elevators
7.1___The passenger elevators are located on an accessible path of travel.
7.2___The passenger elevator doors have a clear opening of not less than 36 inches.
7.3___The passenger elevators have wheelchair-turning spaces that are at least 68 inches wide by 51 inches deep.
7.4___The passenger elevators have controls that are not higher than 54 inches for side approach, and not higher than 48 inches for front approach.
7.5___The passenger elevators have controls that are labeled in raised Braille.
7.6___The passenger elevators serve all public levels of the building.
8. Other
8.1___Notes regarding additional observed barriers are attached.
8.2___Exhibits are attached.
Commercial Fire Doors
16. International Standards of Practice for Inspecting Commercial Fire Doors
16.1 About These Standards for Inspecting Commercial Fire Doors
Many buildings, including schools, high-rises, healthcare facilities, churches, office buildings, factories and warehouses are likely to have fire doors. Should a fire occur, the health, safety and welfare of building occupants and emergency responders depend on the regular inspection of fire doors.
16.2 Purpose
The purpose of this document is to establish international standards for the inspection of commercial fire doors. This document also provides a universal commercial fire door-inspection reporting form.
16.3 Definitions
16.3.1 Fire Door-Specific Definitions
active leaf: the door of a pair of swinging doors that is normally used.
automatic closing device: a device that causes the door to close when activated by a fusible link or heat-actuated device.
barrel: a cylindrical part of a rolling steel fire door that contains the counter-balance springs.
bottom bar: the lower edge of the door assembly.
coordinator: a device used on pairs of swinging doors that causes the inactive leaf to close before the active leaf.
flame baffle: a hinged piece of sheet metal that closes the space between the top of a rolling steel fire door and its hood.
fusible link: a device consisting of pieces of metal held together by solder that melts during a fire.
hood: a sheet metal housing that contains the rolled door.
inactive leaf: the door of a pair of swinging doors that is normally latched.
non-combustible: not capable of igniting when subjected to fire.
sill: the bottom part of a doorway opening; threshold.
16.3.2 Terminology Commonly Found in Commercial Property Inspection Reports
16.4 Goal of the Inspection
The goal of a commercial fire door inspection is to provide an indication as to whether the door is in a state of readiness to perform its intended function during a fire.
16.5 Limitations
It is not the purpose of this Standard to establish inspection procedures to: determine the fire rating or the degree of protection provided by a fire door or surrounding wall; determine the need for a fire door in any particular location; determine proper placement of detectors; determine the functionality of fire-detection systems; heat-test fusible links; determine the combustibility of floor coverings extending through doorways; inspect accordion, folding, hoistway, elevator, chute, access or dumbwaiter doors; inspect fire windows; or inspect fabric fire-safety curtains.
16.6 Optional Add-On Inspection Service
InterNACHI's Standards of Practice for Inspecting Commercial Properties does not require the inspector to perform fire door inspections. The fire door inspection may be offered in conjunction with a complete commercial property inspection or as a separate, stand-alone inspection service.
16.7 Inspection Frequency
Fire doors should be inspected after any incidents that may have damaged the door or its components, or upon noticing possible damage, but not less than annually.
16.8 Visual Inspection
16.8.1 The inspector should visually inspect from both sides of the door assembly.
16.8.2 The inspector should inspect the door opening and surrounding area for potential obstructions, items or conditions that might interfere with the free operation of the door.
16.8.3 The inspector should inspect for auxiliary items that could interfere with door operation.
16.8.4 The inspector should inspect for missing or insecure mounting and assembly bolts.
16.8.5 The inspector should inspect for evidence of field modifications that may void the door’s fire rating.
16.8.6 The inspector should inspect for open holes or breaks that exist in either the door or frame.
16.8.7 The inspector should inspect for failed glazing or glazing beads that are not intact or securely fastened.
16.8.8 The inspector should inspect for missing or broken parts.
16.8.9 The inspector should inspect for combustible sills. Sill should be non-combustible.
16.8.10 The inspector should inspect for clearances of swinging doors between the top and vertical edges of the door and the frame, and the meeting edges of doors swinging in pairs, measured from the pull-side of the door, that exceed 1/8-inch (3.18 mm) + 1/16-inch (1.59 mm) for steel doors, and + 1/8-inch (3.18 mm) for wood doors.
16.8.11 The inspector should inspect for clearances of swinging doors under the bottom of the door that exceed ¾-inch (19 mm), and 3/8-inch (9.5 mm) for doors that have sills more than 38 inches (965 mm) above the finished floor (such as repair counters).
16.8.12 The inspector should inspect the opening of sliding doors at the sides and top for overlaps that are less than 4 inches (102 mm).
16.8.13 The inspector should inspect and note whether combustible floor coverings extend through the door opening, although, depending on the rating of the door, some combustible floor coverings are permitted to extend through door openings. Determining compliance lies beyond the scope of a commercial fire door inspection. Combustible flooring should never extend through doorways protected by three-hour (or greater)-rated fire doors.
16.9 Operational Check
16.9.1 Before checking, the inspector should identify anything that might create a hazard during the operational check. If, in the opinion of the inspector, a hazard might be created by operating the door, the inspector shall not perform the operational-check portion of the inspection.
16.9.2 The inspector should open and close the door using normal operation. Doors should open and close easily.
16.9.3 The inspector should inspect the condition of any gaskets or edge seals.
16.9.4 The inspector should inspect the guides and bearings for lack of lubrication.
16.9.5 The inspector should inspect for blocking or wedging of doors in the open position, or blocked or wedged release arms and weights of sliding and rolling doors.
16.9.6 The inspector should inspect for kinked, pinched, twisted, or excessively worn chains or cables of sliding and rolling doors.
16.9.7 The inspector should inspect the condition of any fusible links and heat–actuated devices (if equipped). Links should not be painted or coated with dust or grease.
16.9.8 The inspector should inspect signs installed on the surface of the fire door for interference with the proper operation of the door.
16.9.9 The inspector should inspect for signage that exceeds 5% of the total area of the face of the fire door to which it is attached.
16.9.10 The inspector should inspect for signs that are attached by mechanical means, such as screws or nails. Signs should be attached to fire doors by the use of adhesive only.
16.9.11 The inspector should inspect for rating and inspection labels and tags that have been painted over. Labels and tags should not be painted over.
16.10 Simulation (Drop) Test
16.10.1 Before testing, the inspector should identify anything that might create a hazard during testing. If, in the opinion of the inspector, a hazard might be created by testing, the inspector shall not perform the testing portion of the inspection.
16.10.2 The inspector should perform all testing and re-setting of the release mechanism in accordance with the manufacturer’s instructions. If instructions are not made available at the time of the inspection, the inspector should continue only if s/he has knowledge and understanding of the operating components of that type of door.
16.10.3 The inspector should inspect for missing closing devices (self-closing or automatic). Every fire door should have a closing device.
16.10.4 The inspector should test any self-closing devices of swinging doors to assure that they close and latch the door completely when operated from the fully-open position.
16.10.5 The inspector should inspect closing mechanisms of swinging doors for hold-open features. Closing mechanisms should not have hold-open features unless they are on doors that are designed to automatically close during an alarm condition.
16.10.6 The inspector should test any coordinators of dual-leaf doors for failure to close the inactive leaf before the active leaf. A coordinator is not needed where each door leaf closes and latches independently of the other.
16.10.7 The inspector should inspect for latching hardware that fails to operate or fails to secure the door when it is in the closed position.
16.10.8 The inspector should inspect for normal operation and full closure of sliding and rolling doors with an initial simulation (drop) test.
16.10.9 The inspector should inspect the closing for speeds slower than 6 inches per second (152 mm/sec.), or faster than 24 inches per second (610 mm/sec.).
16.10.10 The inspector should perform a second simulation (drop) test of sliding and rolling doors to verify that the automatic closing device has been re-set.
16.11 Sample Reporting Language
Commercial Fire Door Inspection Report
Client:
Address:
Location of fire door(s): ______________________________________________________________________
This inspection was performed in substantial compliance with InterNACHI’s Standards of Practice for Inspecting Commercial Fire Doors. It is designed to provide an indication as to whether the door is in a state of readiness to perform its intended function during a fire. Fire doors should be inspected after any incidents that may have damaged the door, or upon noticing possible damage, but not less than annually. A signed copy of this report should be maintained and made available to the authority having jurisdiction, insurance representatives, employees, and other interested parties.
___The inspector was not able to visually inspect from both sides of the door assembly.
___The inspector noted obstructions in the surrounding area that could interfere with the door's operation.
___The inspector noted missing or insecure mounting or assembly bolts.
___The inspector noted auxiliary items that interfered with door operation.
___The inspector noted open holes or breaks that existed in either the door or frame.
___The inspector noted evidence of field modifications that may void the door’s fire rating.
___The inspector noted failed glazing, or glazing beads that were not intact or securely fastened.
___The inspector noted missing or broken parts.
___The inspector noted combustible sills.
___The inspector noted clearances of swinging doors between the top or vertical edges of the door and the frame, or the meeting edges of doors swinging in pairs, measured from the pull-side of the door, that exceeded 1/8-inch (3.18 mm) + 1/16-inch (1.59 mm) for steel doors, and + 1/8-inch (3.18 mm) for wood doors.
___The inspector noted clearances of swinging doors under the bottom of the door that exceeded ¾-inch (19 mm), and 3/8-inch (9.5 mm) for doors that have sills more than 38 inches (965 mm) above the finished floor (such as repair counters).
___The inspector noted overlaps at the sides or top of horizontally sliding doors that were less than 4 inches (102 mm).
___The inspector noted combustible floor coverings extending through the door opening, although, depending on the fire rating of the door, some combustible floor coverings are permitted to extend through door openings. Determining compliance lies beyond the scope of this inspection. Combustible flooring should never extend through doorways protected by three-hour (or greater)-rated fire doors.
___The inspector identified a condition that might create a hazard during the operational check and so did not perform the operational-check portion of the inspection.
___The inspector noted that the door did not open and close easily using normal operating procedures. Doors should open and close easily.
___The inspector noted that the gaskets or edge seals were in poor condition.
___The inspector noted that the guides and bearings lacked lubrication.
___The inspector noted blocking or wedging of doors in the open position, or blocked or wedged release arms or weights of sliding or rolling doors.
___The inspector noted kinked, pinched, twisted, or excessively worn chains or cables of sliding or rolling doors.
___The inspector noted that the fusible links or heat–actuated devices (if equipped) were painted or coated with dust or grease.
___The inspector noted that the signs installed on the surface of the fire door might interfere with the proper operation of the door.
___The inspector noted signage that exceeded 5% of the total area of the face of the fire door to which it was attached.
___The inspector noted signs that were attached by mechanical means, such as screws or nails. Signs should be attached to fire doors by use of adhesive only.
___The inspector noted rating or inspection labels or tags that had been painted over. Labels and tags should not be painted over.
___The inspector identified a condition that might create a hazard during testing and so did not perform the simulated (drop) testing portion of the inspection.
___The inspector noted that the manufacturer’s testing and re-setting instructions were not made available at the time of the inspection.
___The inspector noted missing closing devices (self-closing or automatic). Every fire door should have a closing device.
___The inspector noted that the self-closing devices of swinging doors did not close and latch the door completely when operated from the fully-open position.
___The inspector noted that the closing mechanisms of swinging doors included hold-open features. Closing mechanisms should not have hold-open features unless they are on doors that are designed to automatically close during an alarm condition.
___The inspector noted coordinators of dual leaf-doors failed to close the inactive leaf before the active leaf. A coordinator is not needed where each door leaf closes and latches independently of the other.
___The inspector noted latching hardware that failed to operate or failed to secure the door when it was in the closed position.
___The inspector noted abnormal operation or partial closure of sliding and rolling doors with the initial drop test.
___The inspector noted that the closing speed was slower than 6 inches per second (152 mm/sec.), or faster than 24 inches per second (610 mm/sec.).
___The inspector noted that the second drop test of sliding and rolling doors failed to re-set the automatic closing device.
This inspection was performed by: _________________________
Signature: _____________________________
This inspection report expires on _________________________ (one year from the date of this inspection).
Click for the entire Standards of Practice for Commercial Property Inspections by InterNACHI / COMINSPECT